What is Additive Manufacturing (3D Printing)
Additive manufacturing, commonly known as 3D printing, is a cutting-edge manufacturing process where objects are created by depositing material layer by layer, directly from a digital model. Unlike traditional subtractive methods that involve cutting or milling away from a solid block, additive manufacturing builds up a product precisely and efficiently—reducing waste and allowing for intricate designs. The concept emerged in the 1980s, with the first 3D printer developed by Charles Hull in 1983 using a technology called stereolithography (SLA). Since then, the field has rapidly evolved, giving rise to a range of printing methods capable of producing parts in plastics, metals, ceramics, and even biological materials. Today, additive manufacturing is reshaping industries across aerospace, healthcare, education, architecture, and consumer products, offering a flexible, localised, and sustainable approach to design and production.
It empowers individuals, startups, and industries to innovate faster and manufacture smarter. The future of making is no longer limited by complexity, but only by imagination.
The Principles Behind 3D Printing
At its core, 3D printing is a digital-to-physical process that begins with a virtual design. This design is created using specialised software known as CAD (Computer-Aided Design), or it can be captured using a 3D scanner. Once the design is ready, it is converted into a printable file format—most commonly STL or OBJ—and processed through a slicing program. The slicer divides the model into hundreds or even thousands of ultra-thin horizontal layers and generates the machine instructions that tell the printer exactly how to build each layer.
Depending on the type of 3D printing technology, the printer then begins building the object layer by layer. In FDM (Fused Deposition Modelling), for example, melted thermoplastic filament is extruded through a heated nozzle. In SLA (Stereolithography), a laser selectively cures a liquid resin. Other technologies use powdered materials, binding agents, or even metal melting techniques like laser sintering.
This additive approach allows for an extraordinary level of freedom in design. Complex internal structures, lightweight lattices, and intricate geometries that are impossible with traditional manufacturing can be printed with ease. It also results in minimal material waste since only the required amount of material is deposited. Whether it's a simple prototype or a fully functional end-use product, 3D printing delivers precision, efficiency, and adaptability unmatched by conventional production methods.

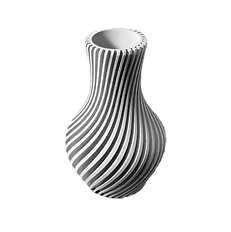

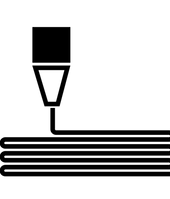
3D Print
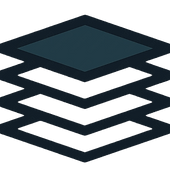
SLICER
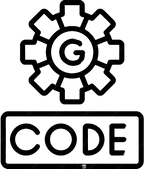
3D Printing Technologies
The History and Evolution of 3D Printing Technologies
The story of 3D printing—also known as additive manufacturing—is one of groundbreaking innovation and continuous evolution. Since its inception in the early 1980s, this transformative technology has redefined the way we design, prototype, and manufacture products across a wide range of industries. From humble beginnings as a tool for rapid prototyping, 3D printing has matured into a powerful suite of advanced manufacturing methods capable of producing everything from medical implants and aerospace components to full-scale houses and consumer goods.
The journey began with the invention of stereolithography (SLA) in 1983 by American engineer Charles Hull, who developed the first process capable of turning digital designs into physical objects using light-sensitive resin. This marked the beginning of the additive manufacturing revolution. As the decade progressed, researchers and engineers around the world began to experiment with new techniques and materials. In the 1990s, Fused Deposition Modelling (FDM) and Selective Laser Sintering (SLS) emerged, opening the door to more robust and accessible 3D printing systems. These technologies brought affordability and practicality to a growing range of applications in engineering, product development, and education.
Throughout the 2000s and 2010s, the field expanded rapidly, with the introduction of metal 3D printing technologies such as Selective Laser Melting (SLM) and Direct Metal Laser Sintering (DMLS), which enabled the production of high-performance parts for use in demanding sectors like aerospace, automotive, and healthcare. Simultaneously, innovations like Digital Light Processing (DLP) and Material Jetting brought new levels of precision and surface finish, making them ideal for dentistry, jewellery, and visual prototypes.
Recent developments have pushed the boundaries of scale and material diversity. Technologies such as Binder Jetting, Multi Jet Fusion (MJF) by HP, and Concrete 3D printing (Contour Crafting) have demonstrated how 3D printing can be applied to mass production, civil engineering, and even sustainable housing. These newer systems have improved speed, part strength, and cost-efficiency—closing the gap between prototype and production-ready manufacturing.
Today, 3D printing is no longer confined to research labs or specialised factories. It is a widely adopted manufacturing solution, integrated into educational institutions, hospitals, construction sites, and consumer markets. Each technology has its own unique strengths, suited to different materials, production volumes, and end-use applications. Understanding the origin and evolution of these technologies is key to appreciating their potential and choosing the right process for the right job.
1. Stereolithography (SLA)
Invented: 1983 by Charles Hull (USA)
Historical significance: The first ever 3D printing technology
Stereolithography was the world's first commercialised 3D printing process. Invented by Charles Hull in 1983, SLA uses a UV laser to cure liquid resin into hardened plastic, one layer at a time. Hull went on to found 3D Systems Corporation, which still manufactures SLA machines today. SLA revolutionised rapid prototyping, allowing product designers and engineers to create accurate visual and functional prototypes much faster than traditional methods.
Today, SLA is widely used in dentistry, medical modelling, and jewellery, due to its ability to produce intricate, high-resolution parts.
2. Fused Deposition Modelling (FDM) / Fused Filament Fabrication (FFF)
Invented: Early 1990s by Scott Crump, co-founder of Stratasys
Historical significance: Made 3D printing more accessible
FDM, patented by Stratasys in 1989, was the first 3D printing technology to use melted thermoplastic filament extruded through a heated nozzle. It became the most widely used method due to its simplicity, low cost, and scalability. When the patents expired in the 2000s, open-source and desktop FDM printers (like the MakerBot and Prusa) exploded in popularity.
Today, FDM is dominant in education, consumer markets, and engineering prototyping, with applications ranging from custom tools to pro
3. Selective Laser Sintering (SLS)
Invented: Mid-1980s by Dr Carl Deckard and Dr Joe Beaman at the University of Texas
Historical significance: Enabled functional, durable plastic parts
SLS was developed around the same time as SLA but took a different approach: using a laser to fuse powdered nylon or other thermoplastics without the need for support structures. This made it ideal for producing complex, interlocking parts and functional prototypes.
Today, SLS is commonly used in aerospace, automotive, and industrial design, thanks to its ability to create strong, precise components suitable for real-world use.
4. Digital Light Processing (DLP)
Invented: Developed commercially in the late 1990s based on Texas Instruments’ DLP projector technology
Historical significance: A faster alternative to SLA
DLP works similarly to SLA but uses a digital projector instead of a laser to cure resin all at once per layer. This makes the process faster and often more affordable. As projector technology improved, DLP printers became compact and precise, entering the consumer and professional market.
Today, DLP is used in dental labs, jewellery design, and miniature figurine production, where speed and surface detail are critical.
5. Selective Laser Melting (SLM) / Direct Metal Laser Sintering (DMLS)
Invented: Early 1990s in Germany by Dr Wilhelm Meiners and Dr Konrad Wissenbach (SLM)
Historical significance: Made metal 3D printing commercially viable
SLM and DMLS are powder bed fusion technologies developed to build metal parts layer by layer. These processes allowed industries to create fully dense metal components with complex geometries impossible through traditional manufacturing.
Today, they are essential in aerospace, medical implants, and high-performance automotive applications where lightweight, custom metal parts are needed.
6. Binder Jetting
Invented: 1993 at MIT by Ely Sachs and Mike Cima
Historical significance: Introduced multi-material and full-colour printing
Binder jetting uses a printhead to deposit a liquid binding agent onto a powder bed (sand, metal, or ceramic), layer by layer. Initially developed for academic research, the technology was later commercialised for industrial applications like sand casting moulds and metal parts.
Today, it is used in construction (concrete printing), decorative ceramics, and mass-customised components.
7. Multi Jet Fusion (MJF)
Invented: 2016 by HP
Historical significance: Improved speed and part strength in polymer printing
Developed by Hewlett-Packard, MJF combines inkjet arrays with heat to fuse polymer powder. It’s significantly faster than SLS and can produce mechanical-grade parts with superior surface finishes.
Today, MJF is widely adopted in mechanical engineering, consumer electronics, and healthcare for functional parts, including prosthetics and orthopaedic gear.
8. Material Jetting
Invented: Commercialised in the early 2000s by Objet (now Stratasys)
Historical significance: Enabled multi-material and multi-colour printing
Material jetting uses printheads to jet photopolymer droplets, which are then cured with UV light. The technology allows printing multiple materials and colours in one build.
Today, material jetting is used in realistic medical models, product design mock-ups, and custom eyewear, providing highly detailed and accurate representations of final products.
9. Laminated Object Manufacturing (LOM)
Invented: Late 1980s by Helisys Inc.
Historical significance: One of the earliest large-format 3D printing techniques
LOM works by laminating layers of material (usually paper or plastic) and cutting them into shape with a laser or blade. Although less precise, it was cost-effective for large architectural or engineering models.
Today, LOM is used primarily in architectural design and educational displays, offering fast and affordable visual models.
10. Concrete 3D Printing / Contour Crafting
Invented: Late 1990s by Dr Behrokh Khoshnevis at the University of Southern California
Historical significance: Pioneered large-scale construction printing
Contour crafting uses a robotic arm to extrude concrete and build walls layer by layer. This method gained attention for its potential to build houses quickly, especially in disaster zones or for affordable housing projects.
Today, it is being used in construction, urban development, and military base infrastructure, with full-scale 3D-printed homes and bridges already built in several countries.
Applications of 3D Printing Technologies
In recent years, additive manufacturing—more widely known as 3D printing—has rapidly evolved from a prototyping novelty to a cornerstone of modern industrial and creative innovation. At its core, additive manufacturing refers to the process of creating physical objects layer by layer from a digital model, using a variety of materials ranging from plastics and resins to advanced metals and biomaterials.
What makes 3D printing transformative is not just the ability to make things—it’s the way it redefines how we make them. Traditional manufacturing methods often involve subtracting material through cutting, drilling, or milling, resulting in significant waste and tooling complexity. In contrast, additive processes are digitally driven, material-efficient, and extremely adaptable, allowing for rapid prototyping, low-volume production, and even large-scale functional parts—without the constraints of conventional design rules.
As we enter the era of Industry 5.0, additive manufacturing plays a central role in reshaping supply chains, reducing carbon footprints, and enabling distributed, localised production. Its applications now span across critical sectors such as:
-
Healthcare: Custom implants, bioprinting, and surgical guides
-
Aerospace: Lightweight structural components and jet engine parts
-
Education: Hands-on STEM learning and design innovation
-
Construction: Sustainable, automated housing
-
Consumer Products: Bespoke accessories, homeware, and smart gadget
1. Healthcare & Medical
3D printing in healthcare has enabled the creation of custom-fit prosthetics, and implants.
orthopaedic devices, surgical planning models, and even bioprinted tissue structures.
Surgeons now use 3D printed anatomical models to practise procedures before
operating, significantly improving surgical outcomes.
Key Applications:
-
Custom-made prosthetic limbs tailored to each patient’s anatomy
-
Dental applications (crowns, bridges, aligners) using resin printing
-
Biocompatible implants (e.g. spinal, cranial) manufactured using SLS or metal AM
-
Patient-specific surgical guides and anatomical models
3D Printed Kidney Model for Pre-Surgical Planning
Surgeons at Guy’s and St Thomas’ NHS Foundation Trust in London made headlines when they utilised a 3D printed kidney model to prepare for a particularly challenging tumour removal procedure. The patient had a tumour deeply embedded within the kidney, in close proximity to vital blood vessels, making the operation highly complex and risky.
To better understand the patient’s unique anatomy, the surgical team collaborated with medical imaging specialists and 3D printing technicians to convert CT scan data into a detailed, life-size model of the kidney, including the tumour and surrounding vascular structures. The model was printed using a high-resolution polymer that could clearly distinguish between different tissue types and anatomical regions.
With the 3D model in hand, surgeons were able to:
-
Visualise the exact location and depth of the tumour
-
Practise and refine their surgical approach prior to the actual operation
-
Identify potential complications and prepare accordingly
-
Enhance communication within the surgical team, as everyone could physically handle and discuss the model
-
Explain the procedure more clearly to the patient, increasing understanding and consent confidence
As a result of this pre-surgical planning using 3D printing, the surgical team reduced theatre time by over 30%, significantly lowering the risk of infection and complications, and improving post-operative recovery.
This case is a powerful demonstration of how 3D printing is revolutionising surgical planning by providing a tactile, patient-specific tool that enhances precision, safety, and patient outcomes.
2. Manufacturing & Industrial Design
3D printing has transformed the manufacturing and industrial design landscape by .
enabling faster, more flexible, and cost-efficient production processes. Traditionally,
the development of tooling, prototypes, and replacement parts could take weeks or
even months. With additive manufacturing, companies can now produce complex
components within days—sometimes even hours—accelerating design cycles and
drastically reducing costs.
The ability to fabricate highly customised, functional parts directly from digital models
has revolutionised how products are developed and maintained, especially in sectors
where rapid iteration and adaptability are crucial. This technology supports lean
manufacturing, minimises material waste, and improves overall production efficiency.
Key Applications:
Tooling and Jigs for Assembly Lines
Manufacturers use 3D printing to produce lightweight and ergonomic jigs, fixtures, and gauges that support precise alignment, measurement, and assembly on production lines. These tools are tailored for specific tasks, improving accuracy while reducing operator strain and manufacturing errors.
Rapid Prototyping for Automotive and Electronics
Automotive companies and electronics manufacturers leverage 3D printing to create functional prototypes during product development. Engineers can test design iterations quickly, enhancing product performance and reducing time to market.
End-Use Parts for Low-Volume Industrial Machinery
Additive manufacturing is ideal for producing low-batch components that are too costly or impractical to mass-produce. Parts can be designed for strength, weight reduction, or specific functional needs, especially when tooling costs for traditional methods are unjustifiable.
Replacement Parts for Legacy Equipment
In industries where certain machines are no longer in production, sourcing spare parts becomes a challenge. 3D printing allows engineers to reverse-engineer and fabricate obsolete components, extending the life of valuable legacy equipment.
Ford Motor Company 3D prints jigs and fixtures for their assembly lines, cutting production lead time by up to 70% and reducing ergonomic injuries.
3. Aerospace & Defence
The aerospace sector has been a pioneer in adopting 3D printing technologies,
recognising the advantages of additive manufacturing for producing high-performance
parts that meet stringent engineering and regulatory standards. In an industry
where every gram of weight impacts fuel efficiency, 3D printing offers an unmatched
capability to produce lightweight, structurally optimised, and functionally
integrated components.
Metal additive manufacturing processes, such as Selective Laser Melting (SLM) and
Electron Beam Melting (EBM), allow for the direct fabrication of aerospace-grade
parts in titanium, aluminium, nickel alloys, and other high-strength materials.
These parts often feature internal channels, lattice structures, and aerodynamic
profiles that are either impossible or prohibitively expensive to produce using traditional
subtractive methods.
Additive manufacturing not only accelerates the design-to-production cycle but also
enables on-demand part production, which is especially useful in space missions,
defence, and remote
aviation operations.
Key Applications:
Lightweight Brackets and Supports
Aircraft manufacturers use 3D printing to produce topology-optimised brackets that are 60–80% lighter than traditionally machined parts while maintaining strength. These components help reduce the overall weight of aircraft, contributing to fuel savings and lower emissions.
Custom Cabin Interior Parts
3D printing allows for the rapid creation of cabin elements such as seat frames, panels, and airflow vents that are custom-fitted, lightweight, and compliant with flame-retardant standards. Airlines can also personalise interiors based on passenger class or specific design themes.
Complex Cooling Ducts for Engines
Aerospace engines benefit from 3D printed cooling ducts with internally routed geometries to manage airflow and thermal regulation more efficiently. These ducts are often produced in one piece, eliminating the need for assembly and improving performance.
Fuel Nozzles Using Selective Laser Melting (SLM)
One of the most cited success stories is GE Aviation’s 3D printed fuel nozzle tip for the LEAP jet engine. Using SLM, the part was consolidated from 20 individual pieces into one, making it five times more durable and 25% lighter. The part handles extreme temperatures and pressures, showcasing the reliability of metal AM in flight-critical systems.
GE Aviation
GE Aviation’s 3D-Printed Fuel Nozzles
GE Aviation has revolutionized jet engine manufacturing by producing over 100,000 fuel nozzle tips using Selective Laser Melting (SLM) technology at its Auburn, Alabama facility. This additive manufacturing approach has significantly reduced part count, improved performance, and cut production costs and waste compared to traditional methods.
Key Highlights:
-
Part Consolidation: The 3D-printed fuel nozzle integrates 20 separate components into a single part, enhancing durability and reducing assembly complexity.
-
Weight Reduction: The nozzle is approximately 25% lighter than its traditionally manufactured counterpart, contributing to overall engine efficiency.
-
Enhanced Performance: The design allows for improved fuel-air mixing, leading to better combustion and reduced emissions.
-
Mass Production: GE's Auburn plant, equipped with over 40 metal 3D printers, has been producing these nozzles since 2015, marking a significant shift towards additive manufacturing in the aerospace industry.
4. Architecture & Construction
Construction 3D printing is an emerging technology that uses large-scale
additive manufacturing systems to fabricate buildings and structural
components layer by layer. Instead of thermoplastics or resins, these printers
extrude cement-based materials, concrete, or earth-based compounds,
forming walls, floors, and structural elements
directly from a digital design.This method streamlines the construction
process by eliminating the need for conventional formwork, reducing
labour intensity, and dramatically cutting material waste. It also allows for
faster build times, greater design flexibility, and reduced environmental
impact—making it an ideal solution for both affordable housing and emergency
shelters in disaster-prone regions.
Key Applications
-
3D Printed Affordable Housing
Entire homes can be printed in 24–72 hours using automated extrusion systems. These are being trialled in regions with urgent housing demands, such as rural Mexico, India, and sub-Saharan Africa. Organisations like ICON, COBOD, and Apis Cor are leading efforts in this space. -
Custom Architectural Models
Architects use 3D printing to produce highly detailed, scale-accurate models that reflect complex geometries and façade designs—supporting design review, client presentations, and urban planning. -
Prefabricated Structural Components
Walls, columns, and panels are printed off-site and transported for rapid assembly. This hybrid approach combines speed and control with quality assurance under factory conditions. -
On-Site Robotics for Construction
Robotic arms or gantry-mounted printers create curved walls and intricate designs not feasible with traditional techniques. These systems are now being integrated with BIM (Building Information Modelling) software for full digital workflows.
Building the Future of Affordable Housing
In partnership with non-profit organisation New Story, American construction tech company ICON made history by developing the world’s first community of 3D printed homes for families living in extreme poverty. Located in Tabasco, Mexico, these homes were printed in under 24 hours each, offering a transformative solution to the global housing crisis.
ICON used its proprietary Vulcan II printer, a gantry-style machine designed to operate in challenging conditions, to layer a specially formulated concrete mix called Lavacrete. This material is durable, weather-resistant, and designed for long-term structural integrity—ideal for tropical climates and disaster-prone areas.
5. Education & Research
Educational institutions at all levels—from primary schools to universities—are rapidly
adopting 3D printing as a central tool in STEM education, creative design, and scientific
research. This technology empowers students to go beyond theory by allowing them to
design, prototype, and test real objects directly from their digital models.
3D printing fosters critical thinking, problem-solving, and practical skills in fields such as
engineering, biology, physics, architecture, and art. It transforms classrooms into
innovation hubs, where students can learn by doing, iterate on ideas, and bring abstract
concepts to life in tangible form.
Key Applications
1. STEM Learning Kits in Secondary Schools
Schools use 3D printers to create engaging kits that support science, technology,
engineering, and maths. These might include:
-
Simple engineering models (bridges, gears, pulleys)
-
Customisable parts for Arduino or micro:bit projects
-
3D puzzles and mathematical solids to teach geometry
Example: Students print components for a solar-powered car or a mechanical grabber as part of a physics module.
2. CAD-to-Print Workflows for Design Students
Design and architecture students learn CAD software such as Tinkercad, Fusion 360, or Rhino to model parts, then 3D print their work for physical testing, scale models, and user interaction studies.
Example: Industrial design students prototype ergonomic product enclosures to assess user grip and function.
3. Scientific Models (Biology, Chemistry, Geology)
3D printing is used to reproduce:
-
DNA double helix models
-
Molecular structures
-
Fossils and bone replicas
-
Internal organs for anatomical study
Example: In biology, students can explore a 3D printed cross-section of a human heart or replicate a fossilised dinosaur tooth in earth science.
4. Robotics & Mechanical Engineering Prototyping
Students can 3D print custom parts for robotics competitions, sensor housings, and mechanical arms. This enhances practical understanding of mechanical systems and electronics integration.
Example: A school robotics team designs and prints lightweight grippers and wheel mounts for a robot in a regional competition
6. Art, Fashion & Design
The art and fashion industries are embracing 3D printing as a transformative
creative tool that allows for previously impossible designs, on-demand production
, and true personalisation. Unlike traditional manufacturing, where tooling, moulds,
and repetition dominate, 3D printing offers unlimited geometric freedom, allowing
artists and designers to break boundaries and experiment with material form and texture.
This digital-to-physical workflow is revolutionising everything from wearable technology
and bespoke jewellery to sculptural installations, lighting, and custom props.
The technology supports both one-off masterpieces and batch production, enabling
both haute couture and mass-market innovations.
Key Applications
1. Custom Jewellery
Designers are using resin and metal 3D printers to create intricate rings, necklaces, and bracelets that can be tailored to each customer’s specifications. The detail achievable in lost-wax casting combined with 3D printed moulds or direct metal printing has revolutionised the fine jewellery industry.
Example: A jeweller in London offers clients the ability to scan their own handwriting or a fingerprint and embed it into a custom ring.
2. Avant-Garde Garments and 3D Printed Textiles
Fashion designers are integrating printed elements into garments, shoes, and accessories, challenging the very definition of textile. These pieces are often shown on runways and exhibitions as wearable art and concept design.
Example: Dutch designer Iris van Herpen famously collaborates with architects and engineers to create couture pieces using laser sintering and stereolithography, worn by celebrities and displayed in museums.
Homeware and Lighting Design
Designers use 3D printing to craft geometric vases, wall hangings, lamp shades, and furniture components. These items often feature complex lattices or interwoven textures that would be nearly impossible to replicate using traditional tools.
Example: A designer uses recycled PLA filament to print zero-waste lampshades with organic spiral patterns, sold via Etsy.
4. Film Props, Cosplay & Theatre
From superhero armour to intricate sci-fi helmets, 3D printing enables quick and accurate reproduction of props and costume elements. The film and entertainment industries use it for rapid prototyping, replica creation, and detailed texture rendering.
Example: Marvel and Star Wars film studios often use SLA and SLS 3D printing to produce screen-ready costume elements and accessories within days.
Dutch fashion designer Iris van Herpen has become a leading figure in the intersection of couture and technology, using 3D printing to create garments that challenge traditional fashion norms. Her runway pieces, often developed in collaboration with engineers and architects, showcase complex geometries and organic forms that would be impossible to achieve using conventional methods. These designs highlight the transformative potential of additive manufacturing in fashion—enabling precise, customised fits, reducing material waste, and allowing for complete creative freedom. As 3D printing becomes more accessible, it is empowering a new generation of designers to experiment with structure, sustainability, and form in ways never seen before.
7. Consumer Products
3D printing is increasingly becoming a mainstream tool for personalised product
creation, empowering hobbyists, makers, and entrepreneurs to design and produce
unique, functional, and decorative objects from the comfort of their own homes or
small studios. With desktop printers now more affordable and accessible than ever,
individuals can create tailored products without relying on mass manufacturing or
overseas suppliers.
From practical household tools to bespoke accessories, the technology allows for
full creative control and on-demand production, reducing waste and inventory.
Thanks to a growing number of online platforms like Thingiverse, Printables,
Etsy, and Shapeways, users can download designs, modify them, or even sell
their own creations directly to consumers.
Key Applications
1. Custom Phone Cases, Bottle Openers, and Keychains
Users can 3D print personalised accessories, often with names, logos, or unique shapes. These items are popular for gifts, promotional branding, or everyday convenience.
Example: A small business prints branded keychains or QR-code bottle openers for marketing events.
2. DIY Gadgets and Smart Home Enclosures
Tech enthusiasts use 3D printing to build custom housings for Arduino and Raspberry Pi projects, IoT devices, and smart home integrations such as thermostat casings and security camera mounts.
Example: A maker prints a temperature sensor enclosure to match their interior design while protecting the device.
3. Replacement Parts for Appliances
One of the most practical uses is printing discontinued or hard-to-find parts for kitchen appliances, vacuum cleaners, or garden tools. This extends product life and reduces e-waste.
Example: A broken washing machine knob is scanned or modelled and reprinted in durable PETG within hours.
4. Decorative Items: Vases, Organisers, and Lamps
Interior decorators and hobbyists design custom homeware that complements specific themes or spaces. The ability to control texture, pattern, and geometry opens up new aesthetic possibilities.
During the COVID-19 pandemic, 3D printing communities across the globe, including hobbyists, engineers, and professional manufacturers, played a vital role in addressing urgent shortages of essential medical equipment. Many individuals and organisations utilised 3D printers to produce open-source designs made publicly available through the National Institutes of Health (NIH) 3D Print Exchange, a platform endorsed by the U.S. Food and Drug Administration (FDA) for emergency use.
These 3D printed items, such as face shields, mask adjusters, ventilator components, and nasal swabs, were critical in supporting frontline healthcare workers when traditional supply chains were disrupted. The designs approved through the NIH platform underwent clinical and technical review to ensure they met minimum safety and performance standards, providing a degree of assurance to healthcare facilities in desperate need of equipment.
Across Britain and around the world, 3D printing enthusiasts collaborated online to share files, improve designs, and coordinate distribution through e-commerce platforms such as Etsy, as well as through direct partnerships with hospitals and care providers. The movement demonstrated not only the flexibility and responsiveness of additive manufacturing in times of crisis but also the power of open-source collaboration to address real-world challenges swiftly and effectively.
This unprecedented initiative during the pandemic highlighted 3D printing's growing relevance as a decentralised manufacturing solution, capable of supplementing traditional production methods during emergencies. It also set a precedent for future applications of 3D printing in public health responses, disaster relief, and humanitarian efforts.
![]() | ![]() |
---|---|
![]() | ![]() |
![]() |
Image from The Hans India: thehansindia.com, Image from Xilloc Medical: xilloc.com


Picture credits Guy's and St Thomas' Hospital
Picture credits Guy's and St Thomas' Hospital
How 3D Printing is Saving Lives during Covid 19
![]() | ![]() |
---|---|
![]() |
![]() | ![]() |
---|---|
![]() | ![]() |
![]() | ![]() |
![]() | ![]() |
![]() | ![]() |
---|---|
![]() | ![]() |
![]() | ![]() |
![]() | ![]() |
---|---|
![]() | ![]() |
![]() | ![]() |
![]() | ![]() |
![]() | ![]() |
![]() |
How Schools Are Using 3D Printing to Revolutionise Learning
![]() | ![]() |
---|---|
![]() | ![]() |
![]() | ![]() |
![]() | ![]() |
![]() | ![]() |
![]() |
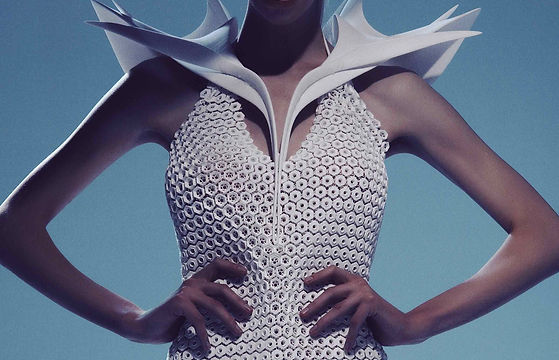
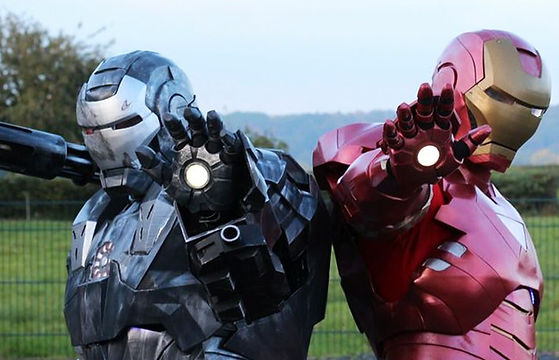
3D Printing in Fashion
Image from: Fashing and Design
![]() | ![]() |
---|---|
![]() | ![]() |
![]() | ![]() |
![]() | ![]() |
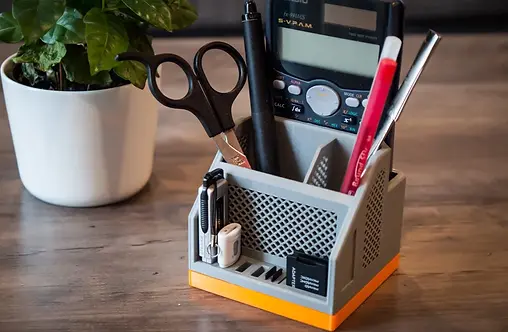
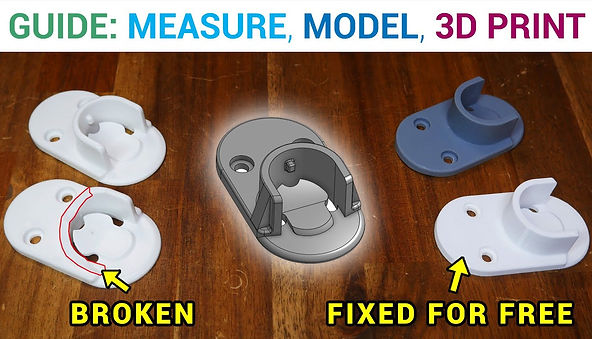
Benefits and Limitations of 3D Printing
Benefits
1. Design Flexibility and Complexity
3D printing, or additive manufacturing, enables the creation of intricate geometries that are often unattainable through traditional manufacturing methods. This capability is particularly advantageous in industries such as aerospace and biomedical engineering, where complex internal structures and lightweight components are essential. For instance, lattice structures can be designed to reduce weight while maintaining strength, which is critical in aerospace applications.Carlos Barraza
Complex lattice structures produced via 3D printing. Source: ResearchGate
2. Rapid Prototyping
The speed at which prototypes can be developed is significantly enhanced with 3D printing. Design iterations can be produced within hours, facilitating faster product development cycles and reducing time-to-market. This agility is beneficial for designers and engineers who require quick feedback on design concepts.
Timeline comparison between traditional prototyping and 3D printing. Source: MarketResearch.com
3. Cost-Effective for Low-Volume Production
For small production runs, 3D printing eliminates the need for expensive tooling and moulds, resulting in cost savings. This is particularly beneficial for custom or specialised products where traditional manufacturing would be economically unfeasible.
4. On-Demand Manufacturing and Inventory Reduction
3D printing allows for the production of parts as needed, reducing the necessity for large inventories. This just-in-time manufacturing approach minimises storage costs and waste, aligning with lean manufacturing principles.
5. Environmental Sustainability
Additive manufacturing is inherently more material-efficient than subtractive methods, as it builds objects layer by layer with minimal waste. Additionally, the ability to produce components locally reduces transportation emissions, contributing to a lower carbon footprint.AspiringYouths
Limitations
1. Material Constraints
Currently, the range of materials suitable for 3D printing is limited compared to traditional manufacturing. While advancements are ongoing, certain applications still require materials that are not yet compatible with 3D printing technologies. This limitation affects the mechanical properties and durability of printed parts.
3D printing materials and their properties.Source: 3D Printer Academy
2. Production Speed and Scalability
While suitable for prototyping and small batches, 3D printing is generally slower than traditional mass production methods. The layer-by-layer fabrication process can be time-consuming, making it less viable for high-volume manufacturing.
3. Surface Finish and Post-Processing
3D printed parts often require post-processing to achieve desired surface finishes and tolerances. Processes such as sanding, polishing, or chemical treatments add time and cost to the production cycle.
4. Size Limitations
The build volume of 3D printers restricts the size of parts that can be produced in a single piece. Larger components may need to be printed in sections and assembled, which can compromise structural integrity and increase labour.
5. Intellectual Property and Quality Control
The ease of replicating designs with 3D printing raises concerns about intellectual property rights and counterfeit products. Additionally, ensuring consistent quality across printed parts can be challenging due to variations in printer calibration and material behaviour.
Insert Video: Demonstration of 3D printing processes and applications.
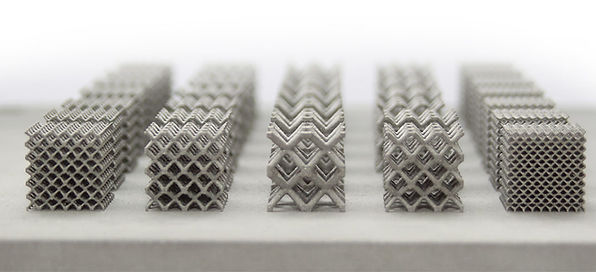

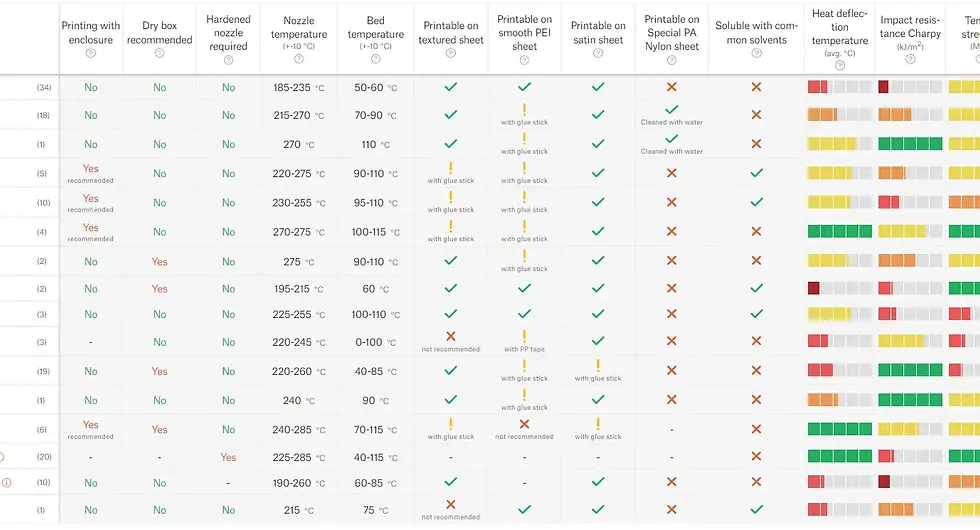
3D PRINTED OBJECTS THAT WILL BLOW YOUR MIND
Materials use in 3D Printing
The choice of material in 3D printing plays a critical role in determining the mechanical performance, surface finish, cost-effectiveness, and suitability of the final product for its intended application. Whether you're printing a functional prototype, a detailed miniature, or an industrial-grade component, the material's characteristics—such as strength, flexibility, thermal resistance, and biocompatibility—will directly affect the part's performance and lifespan.
Each 3D printing material category offers unique advantages:
-
Plastics (thermoplastics) are widely used for general-purpose printing, prototyping, and mechanical parts due to their versatility and ease of use.
-
Resins provide extremely fine detail and smooth finishes, making them ideal for dental, jewellery, and design applications.
-
Metals allow for durable, heat-resistant, and load-bearing parts suited to aerospace, automotive, and medical industries.
-
Composites, which blend base materials with reinforcing fibres or additives, are used to enhance strength, reduce weight, or create specialised properties like electrical conductivity or UV resistance.
By understanding the material properties, users can match the right material to the application, ensuring optimal function, aesthetic quality, and efficiency in both prototyping and production settings.
Thermoplastics
Overview:
Thermoplastics are the most widely used materials in 3D printing, particularly for Fused Deposition Modelling (FDM) or Fused Filament Fabrication (FFF). They are known for their versatility, strength, and ease of use.
Common Thermoplastics:
-
PLA (Polylactic Acid): Biodegradable, easy to print, ideal for prototyping and educational purposes.
-
ABS (Acrylonitrile Butadiene Styrene): Durable and impact-resistant, commonly used in automotive and consumer goods.
-
PETG (Polyethylene Terephthalate Glycol): Combines the ease of PLA with the strength of ABS, widely used for functional parts.
Compatible Printing Methods: FDM/FFF
Industry Usage:
Prototyping, consumer products, educational models, mechanical components.
Resins
Overview:
Resins are liquid photopolymers cured by light, primarily used in Stereolithography (SLA) and Digital Light Processing (DLP) printing. They offer exceptional detail, smooth surfaces, and diverse mechanical properties.
Types of Resins:
-
Standard Resins: Ideal for visual prototypes and detailed models.
-
Tough Resins: Mimic the strength of ABS plastic, suitable for functional parts.
-
Flexible Resins: Used for applications requiring elasticity, such as wearable technology.
Compatible Printing Methods: SLA, DLP
Industry Usage:
Dental models, jewellery, fine-detail prototyping, engineering parts.
Metals
Overview:
Metal 3D printing allows the production of fully functional, high-strength parts often comparable to those made by traditional manufacturing.
Common Metals Used:
-
Stainless Steel: Corrosion-resistant, used in aerospace, automotive, and tooling.
-
Titanium: Lightweight and incredibly strong, critical in medical implants and aerospace components.
-
Aluminium: Lightweight and cost-effective, suited for automotive and consumer electronics.
Compatible Printing Methods: Selective Laser Melting (SLM), Direct Metal Laser Sintering (DMLS), Electron Beam Melting (EBM)
Industry Usage:
Aerospace, automotive, medical implants, industrial tooling.
6. Wax
Primarily used in investment casting, wax-based materials are printed to create highly detailed moulds for metals.
-
Used in jewellery, aerospace, and dental applications
-
Requires clean burnout and precise detail
3D Printed Wax ring models
7. Bioprinting and Experimental Materials
-
Hydrogels and Bio-inks: Used in medical research to print tissue scaffolds and cell structures.
-
Food-Grade Filaments: Chocolate, sugar, and dough can be printed using food-safe extruders.
-
Recycled Filaments: Made from reclaimed plastics, these filaments support sustainable manufacturing efforts.
3D-printed chocolate art
Emerging Materials
Overview:
Recent developments in additive manufacturing have led to the introduction of advanced materials engineered for specific industry demands.
Examples Include:
-
Carbon Fibre-Reinforced Filaments: Exceptional strength-to-weight ratio, used in aerospace and performance sports equipment.
-
Ceramics: High-temperature and wear-resistant, ideal for biomedical and industrial applications.
-
Conductive Filaments: Allow printing of basic electronic circuits and sensors.
Compatible Printing Methods:
FDM/FFF (for composites), Binder Jetting (for ceramics), Material Jetting (for conductive inks)
Industry Usage:
Space exploration, biomedical devices, electronics, high-performance engineering.
4. Composites
Composites combine a base polymer (often PLA, Nylon, or PETG) with reinforcing fibres for added strength and performance.
-
Carbon Fibre Reinforced Filament:
Contains chopped carbon fibre particles, providing high strength-to-weight ratio, rigidity, and thermal stability. Ideal for aerospace, drones, and automotive brackets.
⚠ Note: Requires a hardened steel nozzle due to abrasiveness. -
Glass Fibre Reinforced Filament:
Strong and chemically resistant, used for industrial parts and enclosures. -
Kevlar Reinforced:
Offers excellent impact resistance—used in rugged tooling or wearables. -
Wood-Fill Filament:
Blends PLA with wood fibres, producing a grainy, wood-like texture and even a wood smell when printing. Ideal for architectural models and decorative prints. -
Metal-Fill Filament:
PLA mixed with metal powder (bronze, copper, etc.)—gives a metallic look and feel. Used for statues, awards, and artistic applications.
3D Printed Composite Bracket Versus Machined Steel
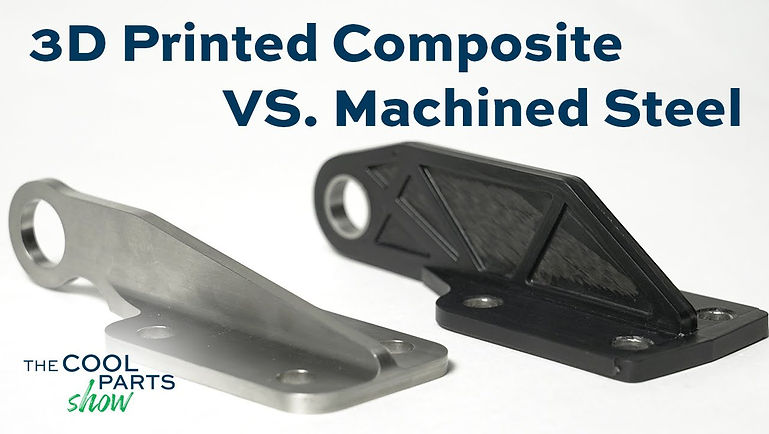
5. Ceramics
Still emerging in desktop 3D printing, ceramic materials (like alumina or zirconia) can be printed and then sintered in a kiln. Ideal for bioinert implants, chemical resistance, or aesthetic tableware.
-
High hardness and temperature resistance
-
Used in aerospace, electronics, and dentistry

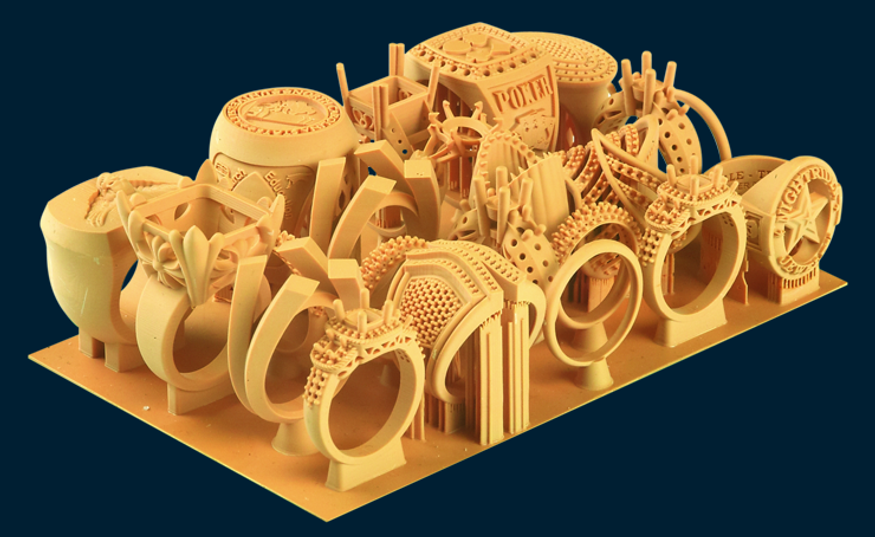

3D Printing Materials explain
Introduction
Choosing the correct 3D printer is a critical decision that can dramatically impact the success of a project, whether for education, prototyping, or full-scale production. The vast array of technologies, materials, and brands available today can seem overwhelming. This guide provides a structured, professional approach to selecting the most suitable 3D printing equipment, highlighting key considerations and profiling leading manufacturers, including Bambu Lab, Ultimaker, and Formlabs.
Different Types of 3D Printers
1. Define Your Application
Before considering brands or specifications, it is essential to first define the intended use:
-
Education:
Priority should be on safety, ease of use, reliability, and low maintenance. Devices must support diverse learning projects, from basic geometric models to mechanical parts. -
Prototyping:
Focus should be on accuracy, speed, and material versatility. Designers and engineers need printers that quickly iterate designs with high fidelity. -
Production:
For end-use parts, durability, consistency, scalability, and certified materials become key. Professional production environments require machines capable of handling long, continuous operations.
2. Key Factors to Consider
Selecting the right printer involves carefully evaluating several technical and operational factors:
FactorWhy It Matters
Print Technology(FDM, SLA, SLS, etc.) Dictates detail, materials, and cost.
Build VolumeDetermines maximum size of prints.
Material CompatibilityImportant for strength, flexibility, heat resistance, etc.
Print ResolutionDefines the detail and surface finish achievable.
Ease of UseEspecially critical for educational or low-expertise users.
Maintenance RequirementsDowntime affects productivity significantly.
Software EcosystemGood slicing software and connectivity are essential.
Support and ServiceReliable customer service and local support reduce risk.
3. Market Leaders: Professional Profiles
3.1 Bambu Lab
Bambu Lab has rapidly emerged as an industry leader by offering advanced, high-speed FDM printers with multi-material capabilities.
Flagship Models:
-
X1 Carbon:
-
Automatic multi-material system (AMS) integration.
-
AI-powered first-layer inspection.
-
Carbon fibre composite compatibility.
-
Extremely high print speed without compromising quality.
-
-
A1 Mini and A1 Combo:
-
Targeted at education and desktop professional use.
-
Affordable yet sophisticated with full automatic calibration and AMS light support.
-
User-friendly UI ideal for students and educators.
-
Ideal for: Prototyping labs, engineering education programs, product design studios.
Bambu Lab X1 Carbon Demonstration
3.2 Ultimaker
Ultimaker is synonymous with reliable professional FDM printing, offering machines well-suited for engineers, architects, and educators.
Flagship Models:
-
S5 Pro Bundle:
-
Large build volume.
-
Automatic material handling and environmental control.
-
Certified material profiles and open material system.
-
-
Ultimaker S3:
-
Desktop-friendly, with dual extrusion.
-
Precision engineering for smaller-scale production and prototyping.
-
Ideal for:
Product design offices, universities, research laboratory Ultimaker S5
3.3 Formlabs
Formlabs transformed the desktop SLA market, delivering industrial-quality resin printing at accessible price points.
🔧 Flagship Models
Form 3+
-
Low Force Stereolithography (LFS) for fine detail and smooth finishes
-
Compatible with over 30 resin types, including biocompatible and engineering-grade
Form 4
-
Latest SLA release with faster print speeds and superior part reliability
-
Optimised for small batch production with high-capacity resin management
Ideal for: Dental clinics, jewellery workshops, medical prototyping, fine mechanical engineering
A professional walkthrough of the Form 3+ capabilities
4. Matching Your Printer to Your Purpose
PurposeRecommended Printer TypeExample Models
EducationReliable FDM printersBambu Lab A1 Combo, Ultimaker S3
PrototypingHigh-accuracy FDM or SLA printersBambu Lab X1 Carbon, Formlabs Form 3+
ProductionScalable FDM or SLA with material managementUltimaker S5 Pro Bundle, Form 4
5. Final Considerations
-
Budget Realism:
Factor in not only printer costs but also materials, maintenance kits, and optional accessories. -
Local Support Availability:
Always confirm that technical support, spare parts, and consumables are available in your region to avoid costly downtime. -
Software and Workflow Integration:
Confirm that the printer's software fits into your existing digital workflows (e.g., compatibility with CAD software, remote monitoring, API access). -
Sustainability and Recycling:
Modern institutions often favour eco-friendly options. Check for filament recyclability and low-energy operation modes.
Insert Photo 5 here:
Title: "Spools of eco-friendly 3D printer filament"
Suggested Image: Neatly arranged colourful filament spools made of recycled material.
Ideal for:
Prototyping labs, engineering education programs, product design studios.

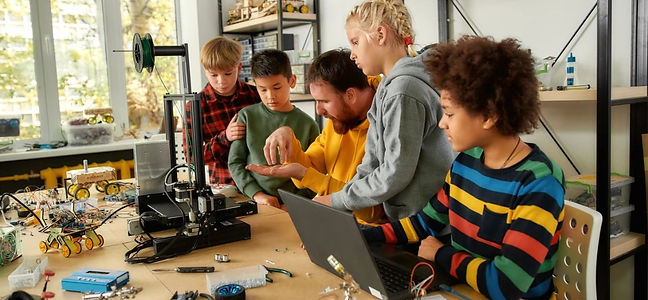

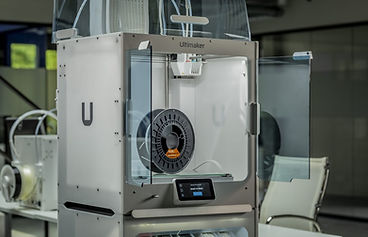
Selecting the Right 3D Printer for Your Needs
Additive manufacturing continues to evolve rapidly, pushing the boundaries of what’s possible in design, production, medicine, and sustainability. The future of 3D printing is not just about faster machines or broader material choices—it’s about redefining how we manufacture, customise, and innovate.
Where traditional manufacturing often relies on subtractive processes and mass production, additive manufacturing enables complex geometries, on-demand fabrication, and mass personalisation at minimal cost and waste. This has opened the door to applications that were once unimaginable—from printing human tissues and organs, to constructing buildings layer-by-layer, to producing lightweight, topology-optimised aerospace components that outperform conventionally manufactured parts.
Moreover, the integration of artificial intelligence, robotics, and smart sensors is transforming additive manufacturing into a self-optimising, intelligent production ecosystem. Machines can now detect errors in real time, auto-correct mid-print, and communicate across cloud networks to improve productivity across global facilities. This digital shift is ushering in a new industrial paradigm, aligned with Industry 4.0.
In parallel, sustainability is becoming a central pillar. New bio-based and recyclable materials, combined with localised, just-in-time production models, are significantly reducing carbon footprints and material waste. Additive manufacturing is enabling closed-loop production systems that support a more circular economy.
As this technology continues to mature, it is not merely supplementing traditional manufacturing—it is revolutionising the way we create, from healthcare to housing, from personalised fashion to autonomous vehicles. The next generation of innovation will be shaped by this powerful convergence of materials science, digital design, and smart manufacturing systems.
4D Printing: Smart Materials That Change Over Time
While 3D printing builds static objects, 4D printing introduces a time-dependent element. It uses smart materials that can react to heat, moisture, or light, allowing printed objects to self-assemble, reshape, or adapt to their environment. This innovation holds great potential in fields like biomedicine, aerospace, and smart textiles, where adaptability and lightweight design are crucial.
Bioprinting: Printing Human Tissue and Organs
Bioprinting is perhaps the most revolutionary application of additive manufacturing. Scientists are now using bioinks—composed of living cells and compatible biomaterials—to print tissues, organ scaffolds, and even skin for burn victims. Although full organ printing is still in early stages, rapid progress is being made in regenerative medicine, offering hope for customised transplants and pharmaceutical testing.
Mass Customisation: Personalisation at Scale
One of the most disruptive trends is mass customisation—the ability to produce personalised products quickly and affordably. From custom-fit shoes and orthopaedic implants to personalised consumer electronics, 3D printing eliminates the constraints of traditional mass production, offering uniquely tailored solutions without increasing cost.
AI and Automation Integration
Artificial Intelligence (AI) is being used to optimise designs and printing processes in real-time. Combined with machine learning and digital twins, this enables predictive maintenance, defect detection, and automated part production—all key to Industry 5.0.
A Sustainable Shift
Future 3D printing will also focus on sustainability, with recycled materials, biodegradable filaments, and closed-loop manufacturing systems. Additive manufacturing allows on-demand local production, reducing logistics emissions and material waste.
The Future of 3D Printing: What’s Next
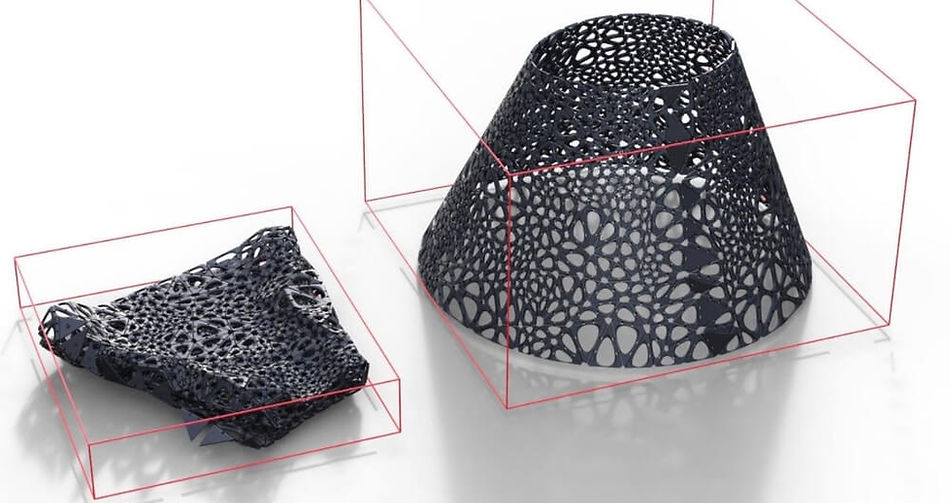
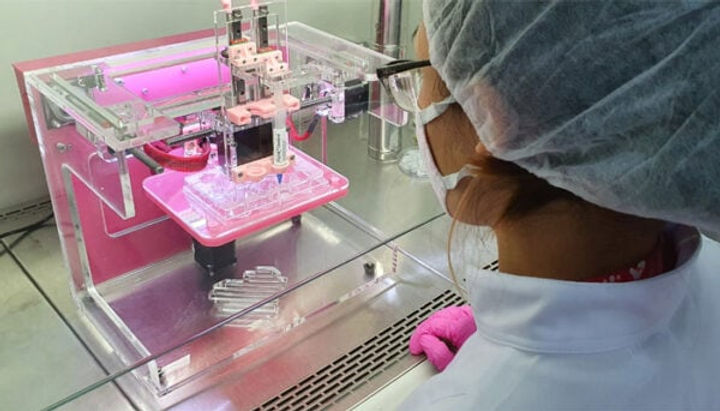
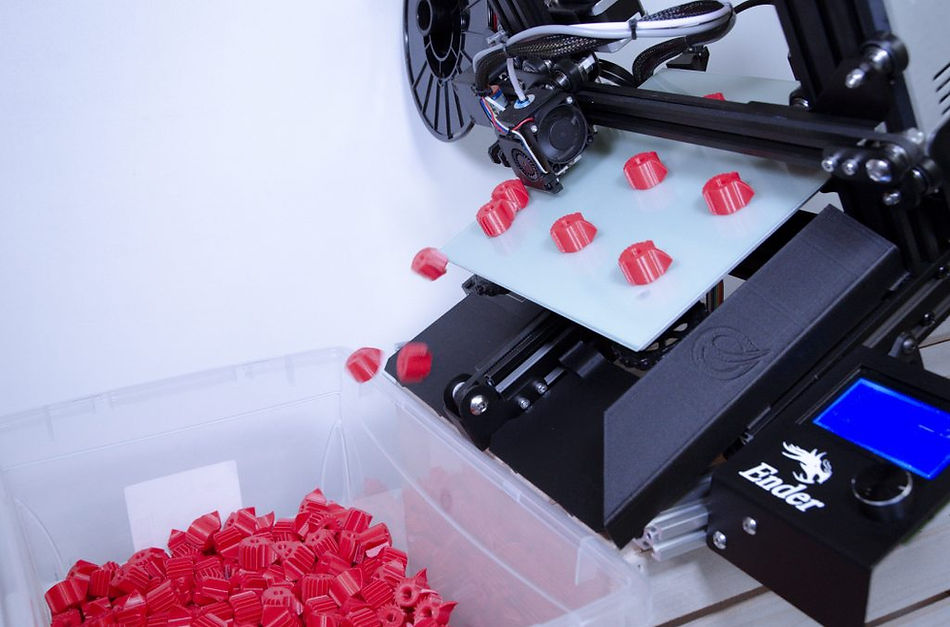
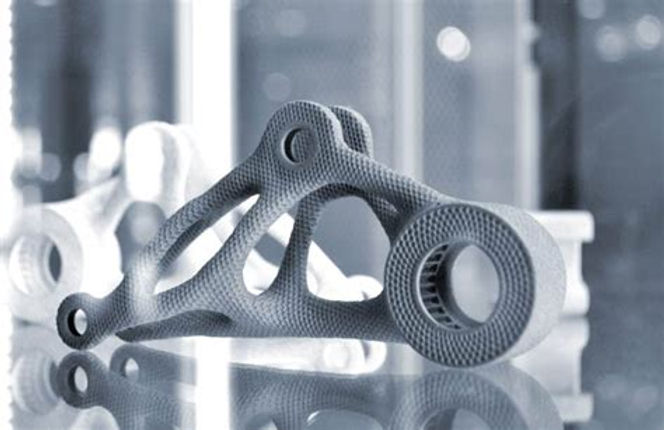
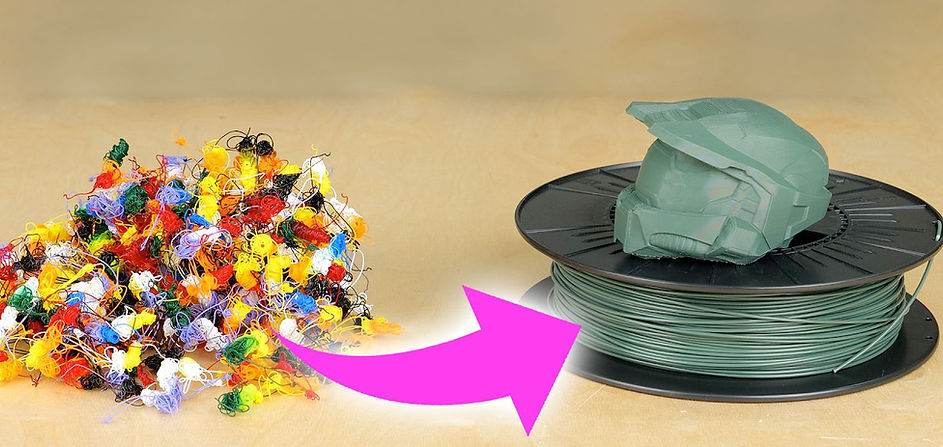
The Evolving Future of Additive Manufacturing
The Future of 3D Printing for Remote and Emerging Regions
The future of additive manufacturing extends far beyond advanced factories and research labs—it’s a game-changer for remote island nations and developing regions across Africa. In areas where supply chains are costly or unreliable, 3D printing offers a decentralised, localised solution to produce tools, replacement parts, medical devices, and even construction components on demand. With a compact setup and minimal infrastructure, communities can now manufacture what they need, when they need it, reducing dependence on imported goods and stimulating local innovation.
📸 Suggested image: A compact 3D printer in a rural or off-grid setup, possibly with local users operating it.
Emerging sustainable materials are making this technology even more accessible. Biodegradable filaments, recycled plastics, and bio-based composites tailored for local climates are enabling environmentally friendly manufacturing that aligns with global sustainability goals. These new materials also support circular production systems—vital for regions where waste management and material scarcity are pressing issues.
📸 Suggested image: Eco-friendly filament spools made from recycled or biodegradable sources.
The integration of artificial intelligence is pushing the limits of what 3D printing can achieve. AI-driven software now optimises designs, predicts potential failures, and automates complex workflows. This makes high-performance manufacturing possible even for those with limited engineering experience, opening the door to smarter, faster, and more resilient production in underserved areas.
📸 Suggested image: Screenshot or interface of an AI-powered 3D printing software or digital twin simulation.
And then there’s the leap into 4D printing—a frontier where printed objects made from smart materials can change shape or function over time in response to stimuli like heat, water, or light. This has enormous potential in places facing environmental unpredictability. Imagine water-activated irrigation parts, temperature-sensitive medical aids, or shelter structures that self-assemble in emergencies. These are not concepts of the distant future—they’re being prototyped and deployed today.
📸 Suggested image: A sequence of a 4D-printed object folding or expanding over time.
Together, these advances signal a powerful shift: additive manufacturing is no longer just a high-tech industry tool—it’s a foundation for resilience, sustainability, and self-reliance in even the most remote communities. This is the future of manufacturing—smart, local, and accessible to all.
What ORIUS3D plan for the future of Additive Manufacturing in Africa
Building a Self-Reliant Innovation Ecosystem in Africa
At ORIUS3D, we believe that additive manufacturing holds the key to a more self-reliant, innovative, and sustainable Africa. Our vision is to localise production, reduce dependency on imported goods, and foster homegrown innovation across the continent. By introducing advanced 3D printing technologies and materials into African markets, ORIUS3D is creating new opportunities for industries, educational institutions, and entrepreneurs to build what they need—where they need it.
We plan to scale access to affordable, high-performance 3D printers and materials specifically suited for Africa’s climate and industrial demands. From agriculture and healthcare to construction and automotive sectors, our goal is to equip businesses with the tools they need to design, test, and manufacture locally. By decentralising production and minimising logistical bottlenecks, ORIUS3D aims to empower a new generation of African creators, engineers, and manufacturers who can drive economic growth from within.
To support this transformation, we are also partnering with local institutions to deliver training programs and develop curriculums focused on digital fabrication. These initiatives will nurture the technical skills needed to sustain long-term innovation and establish Africa as a hub of smart, flexible, and resource-efficient manufacturing.
Advancing Education, Industry, and Impact Through Additive Manufacturing
ORIUS3D recognises that the future of additive manufacturing in Africa depends on education, collaboration, and innovation at scale. Our mission goes beyond selling machines—we’re shaping a knowledge-driven future. We work with schools, universities, technical institutions, and government bodies to embed additive manufacturing into education systems, ensuring students gain practical skills that prepare them for tomorrow’s industries.
Our hands-on STEM workshops and training courses introduce young minds to 3D design, rapid prototyping, and real-world problem-solving. These educational experiences are designed to close the gap between theory and industry, encouraging creativity and technical confidence from an early age. At the same time, ORIUS3D is building strategic partnerships with industrial leaders, start-ups, and research organisations to co-develop local manufacturing solutions tailored for African challenges—such as affordable medical devices, energy-efficient housing components, and sustainable agricultural tools.
As we expand our presence across Africa, ORIUS3D is committed to ensuring access to additive manufacturing is inclusive, equitable, and impactful. Through scalable infrastructure, accessible training, and regional support, we are laying the foundation for a future where African nations lead in innovation, not just consumption. ORIUS3D is not just introducing technology—we are enabling a future shaped by local ideas, empowered by global standards.
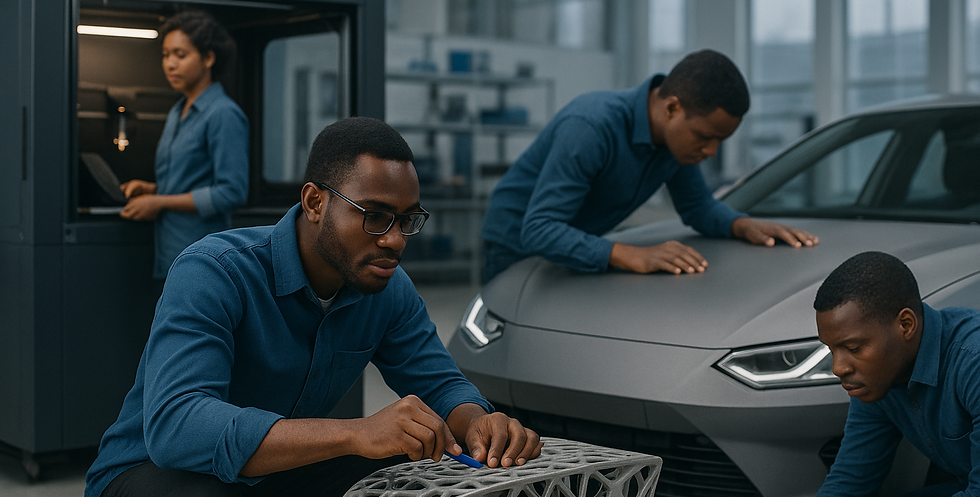